Competences
Welding distortion management with DynaWeld is the virtual testing of component or component group tolerances.
DynaWeld supports you in planning and verification your manufacturing processes for welded assemblies – in industrial series production or in complex and expensive individual components.
We can use our simulation methods to predict geometry deviations of your assemblies in advance. We identify critical areas in your manufacturing concept and help to remedy them. With our simulation, we can ensure the robustness of your production with regard to process parameters, clamping devices or influences of geometric deviations of the intermediate products.
This also includes the determination of permanent residual stresses or microstructure states from the welding process.
WE ARE SPECIALIZED IN THE SIMULATIONS OF:
-
welding structures
-
welding processes
-
heat treatment
-
inductive welding
-
inductive hardening
-
process chains
Our customers:
get broad support in the complex material data generation and the selection of suitable material models, up to ready to go data sets. You benefit from our long-standing experience in specialized simulations – all around the subject of welding and heat treatment.
Industries:

automobile industry
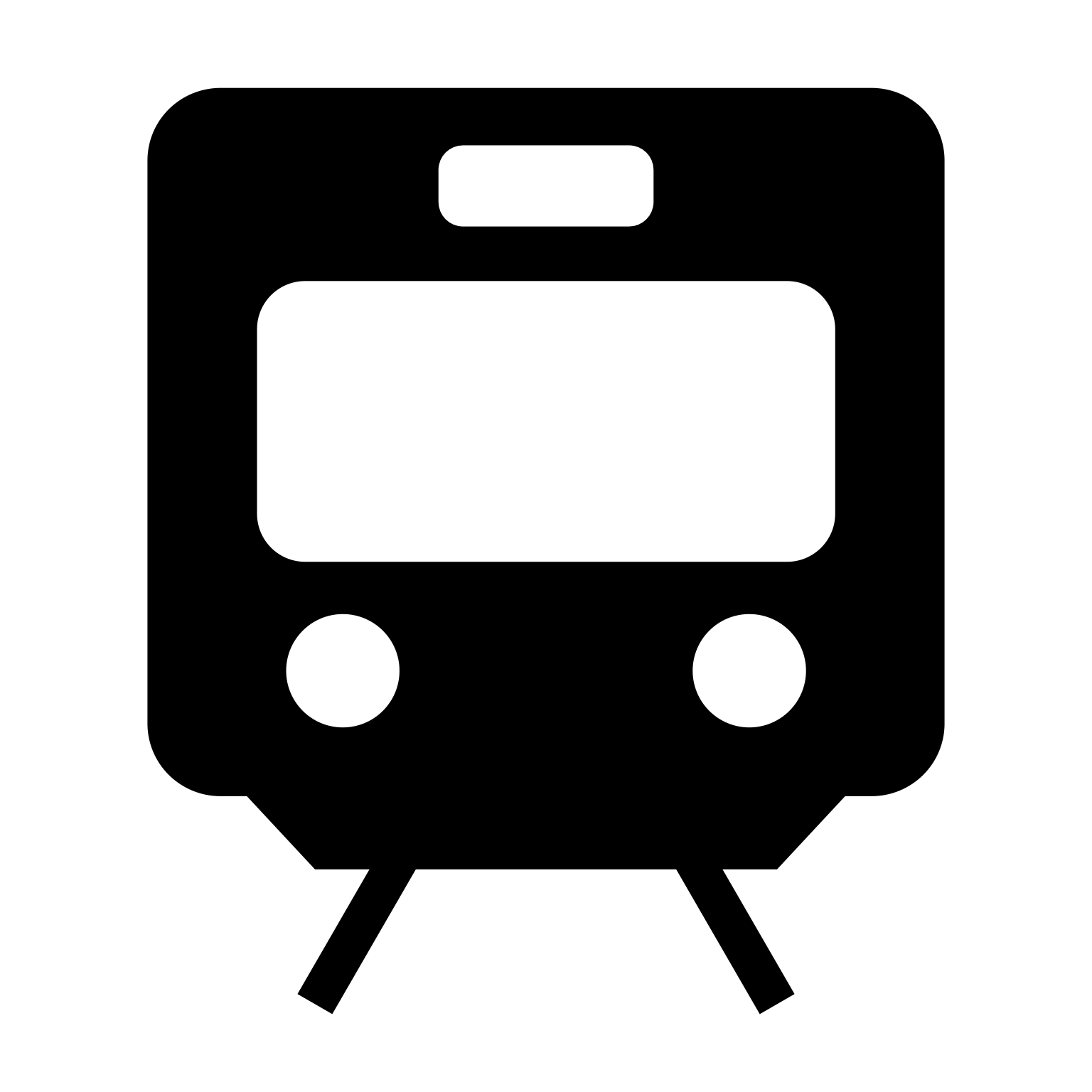
rail vehicle construction
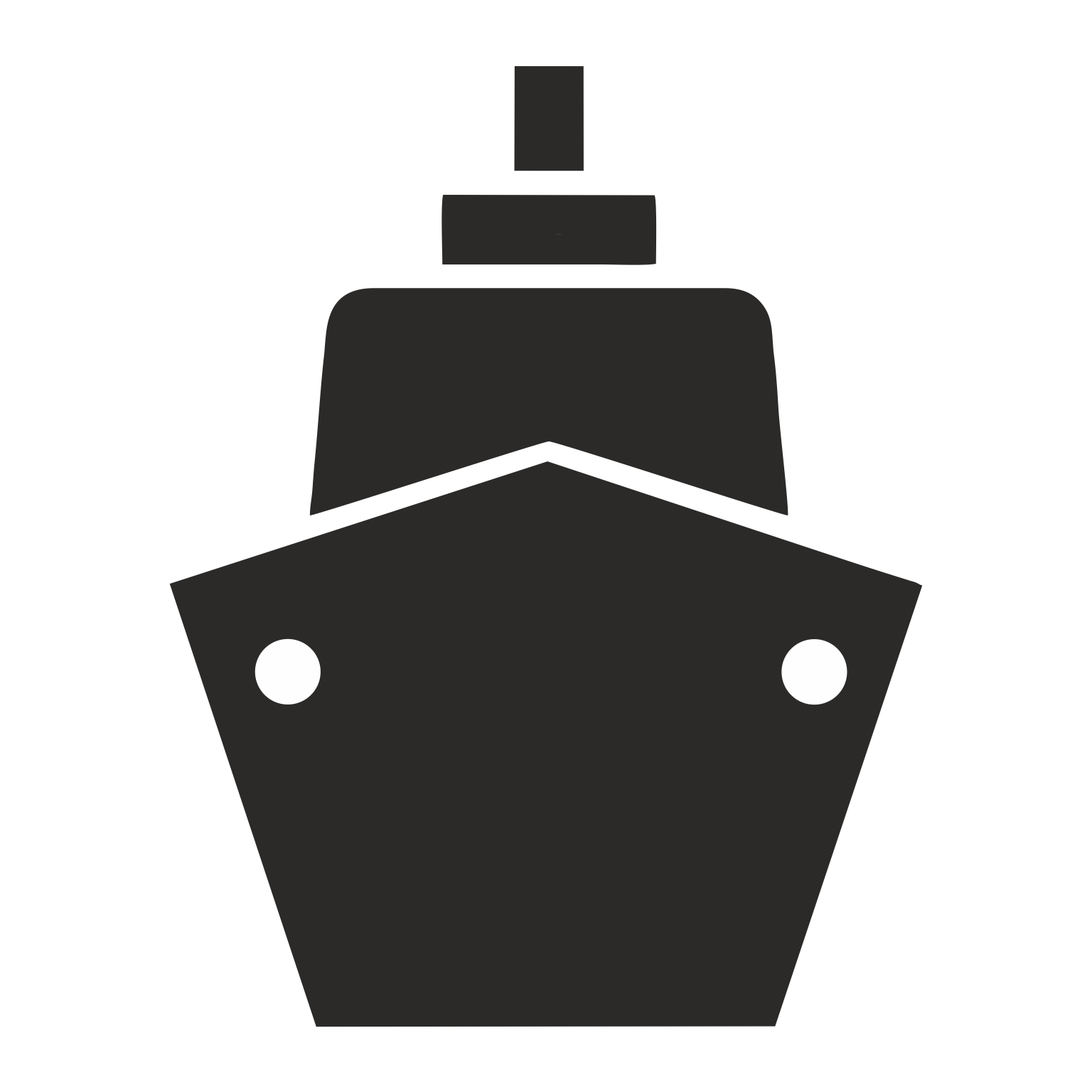
ship constrution
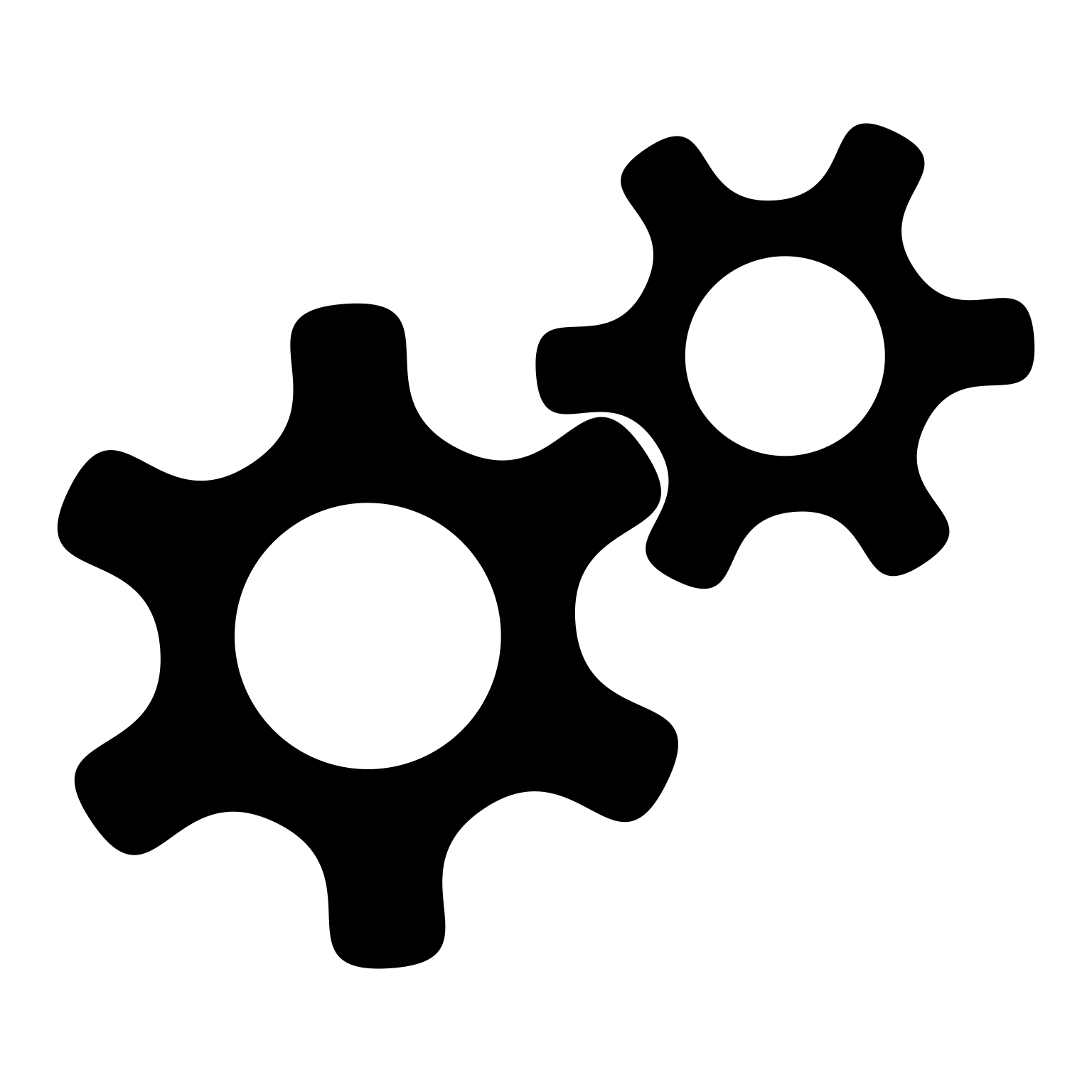
mechanical engineering

construction machinery

medical technology
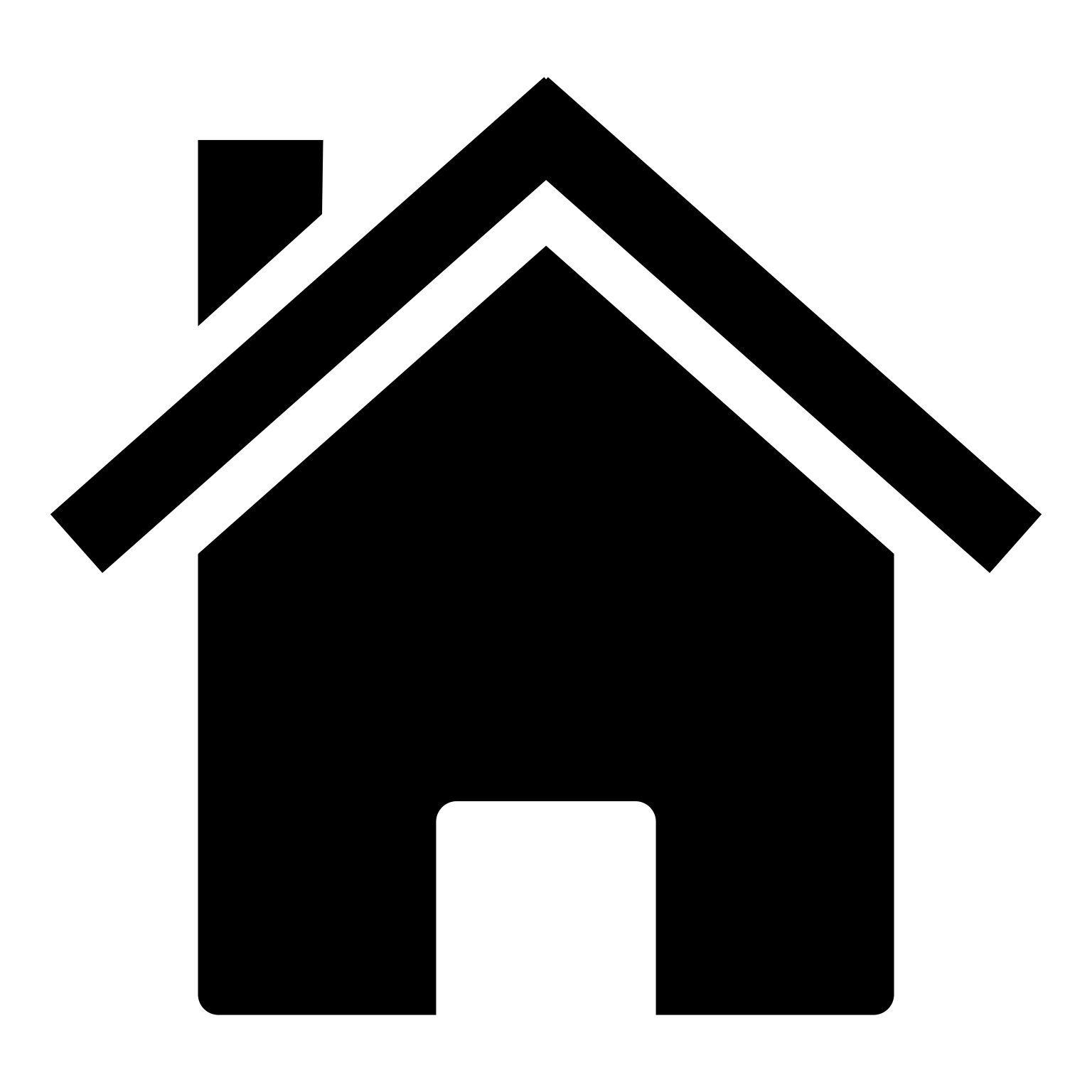
building industry
manual arc welding, inert-gas welding (GMA), TIG welding, submerged-arc welding, laser welding, electron beam welding, hybrid welding, friction welding, resistance welding, resistance spot welding, inductive welding, flash butt welding
blind hardening or quench hardening, case-hardening, inductive hardening, tempering, stress free annealing, heat treatment after welding
Software
We offer the following products:

DynaWeld
Development environment for optimal use of the LS-DYNA code
- Complex simulation models in the twinkling of an eye
- Realization of complete process chains
- Optimized for welding structure simulation and heat treatment simulation
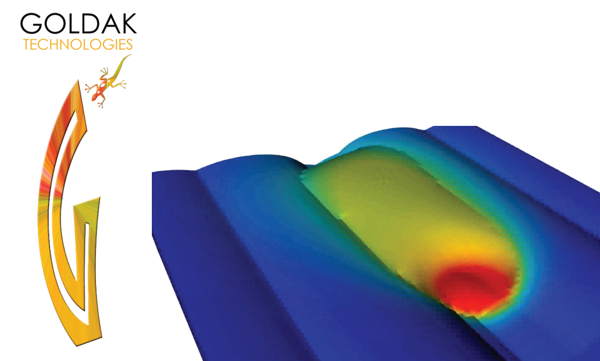
Goldak - VrSuite
from the most experienced professor and most famous researcher for welding simulation
- from the microstructure to the finished component
- the complete spectrum is covered

MatPlusHQ
Heat Treatment made easy
- Determine optimal heating, cooling and holding times for your heat treatment process
- Intuitively operable, even without a Ph.D. in engineering
- Consequence: usually high time and energy savings
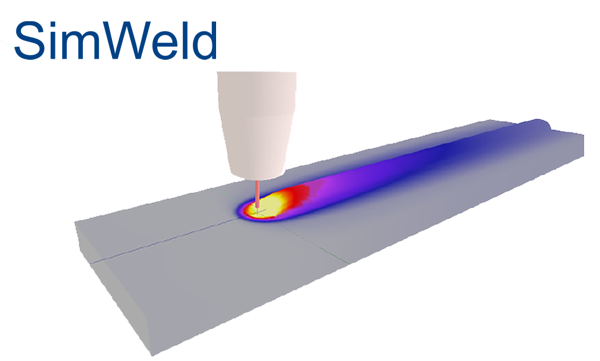
SimWeld®
Process simulation for GMA welding
- Calculation of the melt pool geometry
- Control over weld penetration,pearking and formation of undercut
- Avoiding weld errors
- Results within calculation time less than 2 minutes!

WeldWare®
Welding advisory system
- Calculation of the heat management before welding
- Optimize cooling time, welding parameter, preheating and costs
- Based on one of the largesd librarys on selfmeasured welding-cct-diagrams

individual software
tailored to your very needs
- development of customer-specific software for the calculation tasks:
Welding - Heat Treatment - Process Chain - save costs and processing efforts with our automated software solutions
Services
We have the following offers for you:
-
Welding structure simulation
-
Welding process simulation
-
Resistance spot welding
-
Process chain simulation
-
Simulation of heat treatment
-
Welding technological consulting
-
Customer related software
Benefit from the complete service with model generation, material data gathering, variant comparisons and optimization concepts up to individual partial services.
Our cross-industry customer spectrum ranges from small businesses to large corporations.
Contact us.
We look forward to you.
News Archive
Detect gap formation during welding with DynaWeld welding simulation
Thermal expansions already lead to deformation of the components during welding. This can lead to components moving apart at the joining zone. The formation of this gap endangers process stability and leads to significant shape deviations. This gap formation is to be limited or prevented with a clamp device. Alternatively, tack welds are used to fix the components. With [...]
Induction hardening with DynaWeld
Induction is an efficient method for targeted heating. Components can be heated both completely and partially. Induction heating can be used for welding, straightening, preheating or for heat treatment. We have developed a modeling method to image inductive heating to a 3D model. We use the boundary element method, which means we can do without meshing the air. That [...]
New DynaWeld release available
With the new version of DynaWeld we have prettied up the appearance of the surface. In addition, the user can now choose the colors of the GUI according to his own wishes. In addition to English and German, DynaWeld is now also available in Spanish. At the customer´s request, we can now enter any language. Other functionalities: Simplified [...]
DynaWeld for heavy machinery construction – heat management during welding
Heavy machinery construction places special demands on the design of welded joints. Solid components with sheet thicknesses between 100 mm and 500 mm absorb the welding heat much faster than thin-walled components. The result is high cooling rates with common welding processes such as gas-shielded metal welding or submerged arc welding. Steels that can be welded in the thin [...]
Validation tests for the welding simulation
DynaWeld at the Technology Institute for Metal & Engineering GmbH (TIME) The prediction accuracy of numerical simulations can only be convincing if the models used are suitable for the physical processes and the modeling is realistic. A check can be done on the basis of welding tests. So far, one can find in the literature for verification purposes [...]
DynaWeld at INSIGHT @ Volkswagen Wreśnia 2019
INSIGHT @ Volkswagen Wreśnia 2019 was hosted by the Automotive Circle and took place in Poznan. Highlight: Visit to the new VW plant for the Crafter in Wrenia. In addition to many interesting lectures on body construction with a focus on commercial vehicles, DynaWeld is contributing to digitalization in production planning: Distortion managemnt in the design of the [...]
Office North
Hermann-Löns-Str. 3a
D-21382 Brietlingen
Phone: +49 (0) 4133 400 88 63
Fax: +49 (0) 4133 400 73 35
Mobile: +49 (0) 178 426 04 73
E-Mail: rohbrecht@dynaweld.de

Office Kamen
Herbert-Wehner-Straße 2
D-59174 Kamen
Mobile: +49 (0) 176 801 484 35
E-Mail: prehm@dynaweld.de
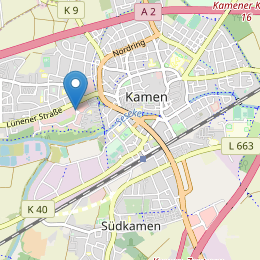